That last question is the focus of a partnership between researchers at Hamilton’s McMaster University and Vancouver-based Vitacore, a producer of personal protective equipment. This month, they launched a pilot project that sees Vitacore collect and sanitize used PPE, and McMaster’s Centre of Excellence in Protective Equipment Materials assess how best to recycle it.
PPE is essential to fighting COVID-19, but much of it is single-use plastic. In October, the federal government projected that, in 2021, approximately 63,000 tons of COVID-19-related PPE would end up in landfill. That’s why, when it came time to formalize CEPEM (which informally launched to support a nascent Canadian PPE supply chain in March 2020), Ravi Selvaganapathy wanted sustainability to be one of the centre’s core priorities.
We speaks with Selvaganapathy, a professor of mechanical engineering and the centre’s director, about his team’s work to recycle masks — and its larger quest for sustainable PPE.
We: My understanding is that up to 30 faculty have worked at CEPEM and that you worked with around 40 different companies to get PPE made. At what point during production did you start thinking about recycling?
Ravi Selvaganapathy: Around July was when we thought that we should put together the centre. Until then, it was a volunteer effort. I realized that, well, this is all going to go into dumps to be another source of pollution in the environment. We figured that, as a university, we should look at long-term sustainability on an industry-wide basis.
We knew that that was a big challenge, because it’s fairly low-cost and easier to produce these materials out of non-biodegradable products or petroleum products. It’s more difficult to do it using sustainable materials.
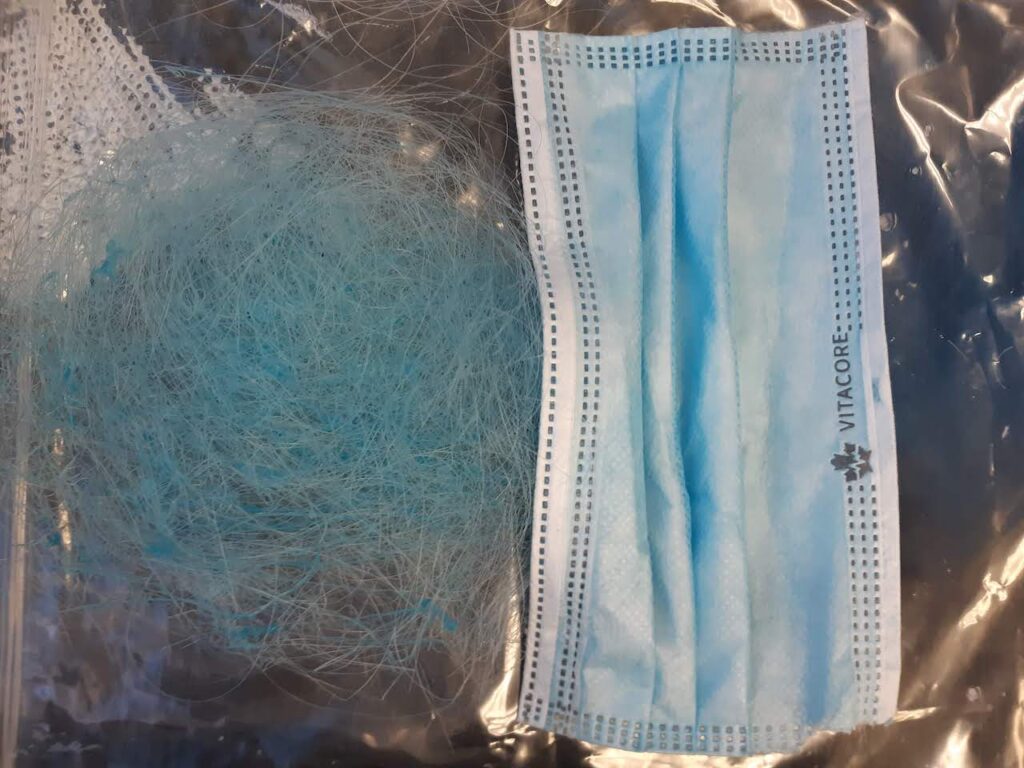
We: A lot of the work your team has done has been to make PPE out of those more sustainable materials, correct?
Selvaganapathy: Yeah, exactly. In terms of sustainability, we have four subcategories, one of which is to look at the PPE that are currently there and then to recycle them. The next thing is to change the materials themselves from non-biodegradable to biodegradable. There are a number of polymers that are biodegradable and will decay over a year or two in the environment.
Another thing is to use natural polymeric materials. Canada is well-endowed with paper and pulp and wood products. Cellulose is a very interesting material. It doesn’t have the right filtration properties now. But we could develop new manufacturing processes to make things like cellulose and cotton in a way that they perform very well as a filter material.
And the fourth area is to assist manufacturers of equipment who do disinfection and re-use of PPE. There’s a growing interest, where, instead of having a disposable product, what you have is almost a wearable product. You can spend more money on it, but then you reuse it for three months or six months or so, either by washing or by other decontamination techniques.
We: I guess this partnership with Vitacore would fit into that first bucket: recycling.
Selvaganapathy: Exactly. Vitacore is very interested in looking at a system in which they would position collection bins in hospitals, collect these products (those bins will have disinfection agents in them); once they are collected, they will be processed. Where we are helping them is by looking at the processability of these materials.
The initial pilot aspect of it is that Vitacore will collect PPE in a few locations in Vancouver and then sterilize it and send it over. Then what we will do is look at processing and extruding it. What we want to find out is if there is a simple production-type system that we can develop in which we can look at the rheological properties and identify what needs to be added to get to the right properties so that it can be extruded into fibres that can go into composites. [Rheology is the study of how matter flows. When extruding plastic, its application helps engineers understand how material will melt and what additives can achieve certain properties.]
We: I read that the PPE can be melted down into fibres and into pellets and that that sort of thing could then be used to reinforce concrete.
Selvaganapathy: Yes, it could be used as a potential reinforcer for concrete. Also, if you look at the construction area, a new emerging building material is actually processed wood. Fibre-reinforced composites are extremely good. [Recycled PPE] could be a material that could be beneficial for that purpose. It provides excellent insulating properties, as well as structural properties, but it is reprocessed material from something that would have normally gone into the environment.
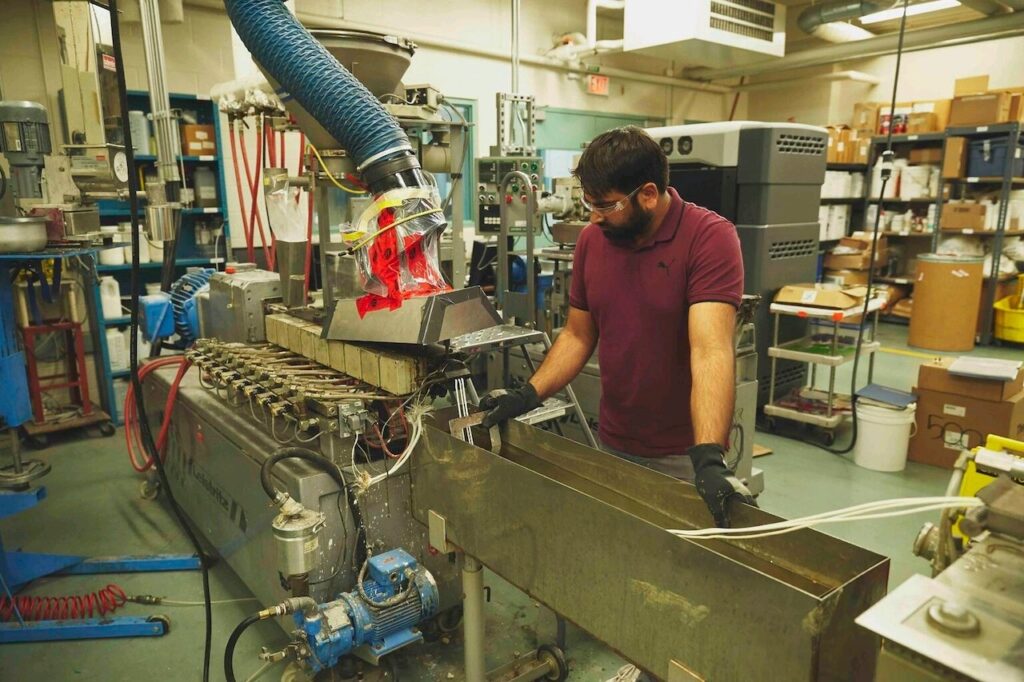
We: What are some of the challenges in coming up with what the recipe [to recycle the material] is going to be?
Selvaganapathy: I think the biggest challenge is the variability of the materials. There are hundreds of different mask manufacturers, and each one uses slightly different materials. And in this reprocessing, what you’re going to get is a variability in composition that comes in. The challenge is in quickly identifying what the variability in composition is without expensive techniques. And, ultimately, this process has to be lower in cost than using virgin polymer. Otherwise, the industry is just going to go and use virgin polymer and continue to have an impact on the environment. That’s not what we want.
We: What sort of timeline are you looking at with the research for this partnership?
Selvaganapathy: It all depends on the kind of resources that we can deploy. We’ve already done some initial testing. We could basically reprocess masks manufactured by Vitacore and extrude fibres from them. Our next step is to have a variety of masks mixed in and then do the reprocessing. We’re also in the process of incorporating that into concrete. We’ve done some preliminary tests. There are some additives that we need.
Essentially, this has to be funded, and if it is funded the right way, then in a year’s time, we should be able to reprocess this at a reasonable scale. Of course, at the end of the day, the cost is a big factor. If you are able to achieve the cost, then I think scaling up to multiple locations across Canada should not be an issue.
We: I suppose that would be particularly important. I mean, the federal government projected 63,000 tons of COVID-19-related PPE would end up in landfill in the next year. Certainly, that would require a lot of processing.
Selvaganapathy: Absolutely. I think all of this comes down to putting a price on the disposal of these environmentally contentious sort of products. If there is no price on disposal, it’s going to be continuously disposed of, and virgin material is going to be used. But if there is a price on it, that can be redirected to reprocessing.
We: Is there anything that we didn’t talk about that you wanted to bring up?
Selvaganapathy: The reprocessing is just one aspect. That’s what I want to emphasize. We are also exploring with other partners how to look at biodegradable polymers, but, more importantly, natural polymers like cellulose. And if that comes through, then that is a very renewable resource — and a degradable resource. That would have less of an economic challenge in bringing to the market as compared to, say, a carbon price on PPE, for example. That’s one thought.
Another is the reusability of the PPE. We are looking at PPE not as a disposable material but as something that you will have and use whenever you have a sniffle, as long as the filtration properties are good. There’s not going to be one solution; it’s going to be multiple solutions that will bring environmental sustainability to this field.
This interview has been condensed and edited for length and clarity.